车门窗框总成的辊压成形
窗框分总成中的上窗框、后窗框及玻璃导轨等零部件,因其断面结构(见图2)的复杂性和功能要求的特殊性,它的开发制造很难通过冲压成形的方式实现,多采用辊压成形与其工艺相结合的方式进行生产制造。

窗框总成的制造工艺流程大致可分为:带料的开卷→成形机组辑压成形→轮焊机焊接→辐弯机组辑弧→切断→拉弯成形→冲压→切角→组焊→打磨一→矫形。其中成形机的辑形是整个辑压工艺的重点,通过开发一系列辊轮并安装固定在成形机组上,带料在辊轮的作用下,逐渐成形至设计所需的断面结构。
轮焊机焊接主要是通成过对辑压成形后的制件等距设置一 些焊点,以防止成形后产品截面的展开。
辊弯机组辑 弧与拉弯成形工序都是解决制件的弧度问题,但它们有着本质的区别,辑弯机组辐弧主要是把制件由直线形状成形为曲线形状,它们是在一个平面内的曲率变化,而拉弯成形是由拉弯机配合专用拉弯模可实现制件变曲率的三维空间弯曲成形。
拉弯成形后根据制件的工艺需求,往往还需进行冲压、组焊及矫形等作业内容。
以图2所示的前门窗框总成为例,窗框总成由多个辑压制件和冲压片件拼焊组成。
根据它们的几何构造,总成零件在组焊完成后由于制件公差的累积和焊接应力释放等原因,致使总成零件容易出现扭曲、回弹等质量缺陷,一方面影响到车门总成与侧固、翼子板等车身搭接零部件的型面匹配和与门洞之间的间隙匹,另一方面也会影响到车门内部车窗玻璃的自由升升降,致使车窗玻璃上下滑动时卡顿并出现异响。
基于窗框总成的结构特性和重要的装配关系,制造精度和一致性就成为窗框总成制造工艺的重点和难点,也需作为关键工序进行重点管控。
尤其开放式u型结构的窗框,扭曲、回弹的控制就更加困难,为了保证窗框成品的质量及稳定性,除了对工、辅器具进行合理、优化的设计,制造外, 在窗框制造工艺的设计 上,需考虑在组焊工序后增加一道人工矫形的辅助工序,着重解决制件的扭曲、回弹问题,以达到设计所需的功能要求。
总成零部件的焊接
门总成是由多个零部件、多种工艺、多道工序拼焊组成。
焊接工艺流程较为复杂,如图3所示,整个车门的焊接生产过程涉及凸焊、点焊及C02气体保护焊,焊点多,有双层焊,也有3层焊。
实际生产过程中,焊接工艺影响到的因素很多,既有因焊接变形而致使总成零件几何尺寸超差的情况,也有因焊接工艺参数不合理等原因造成凹坑、咬边、烧穿、未熔合等焊接外观缺陷的产生,很大程度上影响到产品的质量和生产的效率。
为了保证总成焊接的质量要求,一般需从以下几个方面加以管控。
(1)焊接夹具的合理、可靠性
在焊接的过程中,夹具工装的主要作用就是将各个焊接组件进行准确定位后可靠夹紧,并保证组焊总成的结构精度要求。夹具的设计开发除了依据生产节拍设定合理的焊接工序外,还需根据组焊制件的具体形状、外形尺寸及公差要求,结合焊接实际生产过程中焊枪电极压力大小、焊点接头区域的应力应变及生产操作的适应性等因素,合理设计夹具的结构形式、定位方式和夹持部位。既要保证定位和夹持元件对制件的定位准确,又要使夹持元件和定位元件具有足够的强度和刚度,保证制件投取准确、质畅,有效地防止制件在装配、压紧和焊接过程中出现变形,影响制件的焊接质量。
(
2)焊接工艺参数选取
焊接参数的选取是整个焊接工艺的核心,工艺参数选取正确与否直接会影响到总成产品的焊接质量。在门总成焊接工艺中,虽然有凸焊、C02气体保护焊,但点焊用得最为广泛,尤为重要。在点焊工艺中,电极压力、电极接触面的直径、焊接电流、通电时间等参数都会对总成焊接的质量产生直接影响。
点焊过程中一般优先采用大电流、短通电时间的工艺参数,也称为硬规范,这种工艺参数的选取具有电极磨损小、生产效率高,焊件表团压痕浅,焊接变形小,外形美观等显著优点。
但是,由于焊接电流大,通电时间的掌控就必须精确,否则,就很容易引起加热不足或过烧,严重影响到焊点的焊接强度。
另一方面,电极压力的大小也会对焊件的焊接质量产生影响,电极压力过大将会使接触电阻减少,电流密度也会随之减小,致使焊件加热不足,焊核小,焊点强度低,甚至可能形不成焊核;
但当电极压力过小,将会使接触电阻加大,电流密度随之变大,从而引起焊件烧穿,产生严 重喷溅。
除此之外,电极头接触面直径的大小也会影响到总成的焊接质量,电极头直径越大,电流密度会相应变小,导致焊接熔核直径变小;
但若电极头直径过小,电流密度就会加大,焊接时会发生飞溅、火花,压痕大且深,也会影响到焊点的焊接强度。
所以焊接工艺参数必须根据板材厚度、材质等合理、规范的选取,如表1所示,以保证良好的焊接质量。
涂胶与包边
由于车门总成属于闭合件,为了保证车门总成的密封防锈、减振降噪等性能要求,提升整车的舒适性,在制造过程中需对门内外板进行涂胶和包边工艺处理。
根据门总成涂胶的工艺要求,→般涂胶分为折边胶和膨胀胶两类,如图4所示。
车门外板属于外覆盖件,因其严格的外观要求而禁止焊接,但内外板之间仅仅依靠包边这种物理连接的方式,往往会出现连接强度不够的情况,需要在包边工序前对门外板的内表面周边区域用打胶枪或涂胶机均匀涂布折边跤,内外板压合包边完成后,折边胶充分填充到内外板之间,代替焊点起到粘接、连接的作用,从而增强门内外板之间的连接强度。
膨胀胶一般涂抹于门外板的支撑件或者加强梁上,受热膨胀后门外板 与整个支撑件或加强梁紧密粘合在→起,以达到汽车在高速行驶过程中的减振作用和发生碰撞时的缓冲作用,同时减少振动产生的噪音。
车门包边是车门总成制造过程中比较特殊的工艺方法,包边后要求外表面平整、光)I顷,无压伤、凸包、凹坑等外观质量缺陷,同时还需要保证车门型面和包边区域整体尺寸精度的稳定。
所以,除了对设备、工装提出很高要求外,还对门内外板的品质及包边工艺数据的处理提出了很高的要求。
(
1)门内外板包边位置问隙保证
门内外板包边位置间隙需均匀、合理,→般控制在2. 0~3.0mm,如罔5所示。若间隙过小,门外板翻边 到45°弯曲时,就会碰到门内板的凸缘边,使门外板翻 边弯曲受到限制,表面材料受到拉力作用,刚性较差的形状面就会产生凹陷。若间隙过大时,则容易出现 包边塌边。
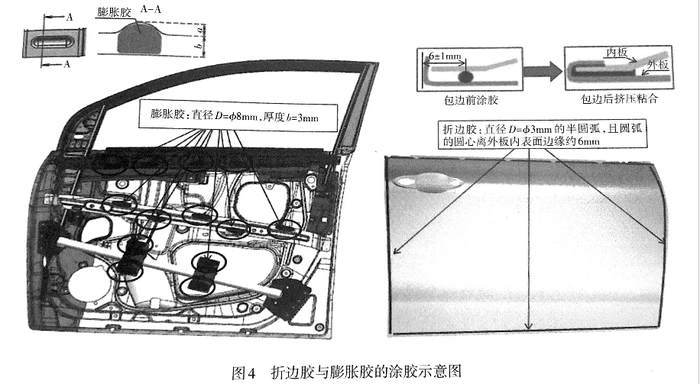
(2)材料蠕变的工艺补偿
在包边过程中,板材因塑形变形致使门四周的轮廓尺寸发生一定的变化,往往会收缩0.1~O.Smm,根据门外板的材质、翻边R的大小及包边方式的不同各有差异,如图5所示。为此,在设计外板翻边工序时,对外板的轮廓需向外做过翻边工艺处理。转角等特征线部位补偿设定为O l~0.2mm,一般部位补偿为0.3~O.Smm,若是滚边机器人包边,变化的补偿量要稍小→ 些,补偿值一般控制在0~0.2mm范自内。
( 3
)门外板拐角处的包边尺寸要求
车门包边时,拐角处最容易产生包边不顺、不圆滑或者是包边不全等质量缺陷,主要原因是拐角处多 料或少料所致。为了保证门角部的包边质量,在门外板制造时,其边线及翻边高度的设计要进行综合考虑,具体边线尺寸要求如图6所示。
|